Heliosand, a startup from Lyon, is transforming toxic waste disposal with a solar-powered system that reaches 4,000 °C and turns dangerous materials into reusable construction elements.
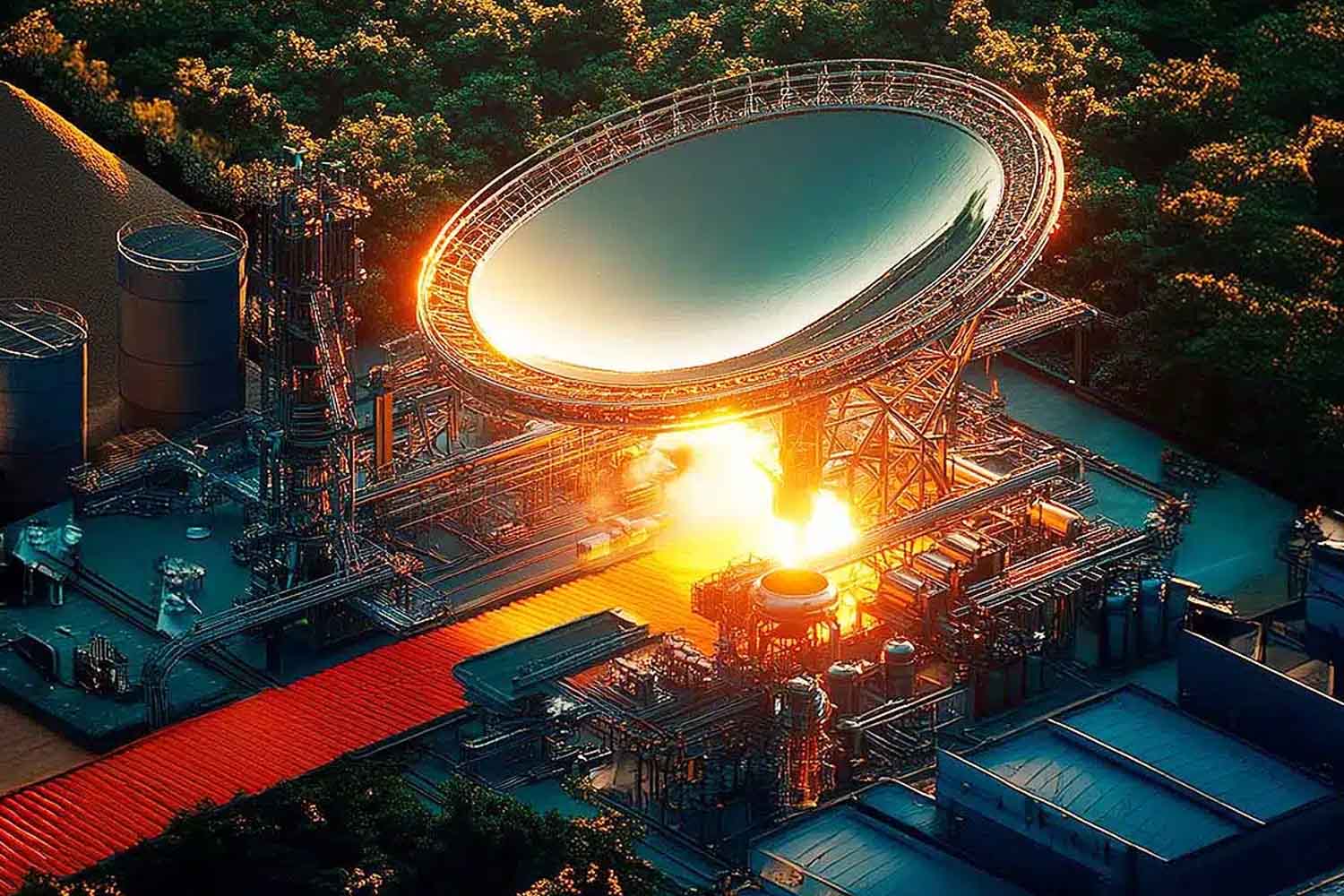
©Heliosand
Asbestos, dredging sludge, bauxite residue, fluorinated waste. These are some of the most problematic types of industrial waste — often labeled as non-recyclable and extremely hazardous to both human health and the environment. Traditional disposal methods like incineration and landfilling not only devour huge amounts of energy, but they also leave behind long-term environmental risks and pollution.
But a young French startup, Heliosand, headquartered in Lyon, has developed a zero-impact technology that’s poised to upend the way we think about these toxic leftovers. Their idea? Use the sun to destroy hazardous waste — stripping it of its toxicity and transforming it into reusable, stable resources.
The power of a 100-square-meter lens
At the core of Heliosand’s innovation is a massive solar concentrator, equipped with a 100-square-meter (approx. 1,076 square feet) Fresnel lens — a behemoth that harnesses sunlight to reach temperatures of up to 4,000 °C (7,232 °F). That’s hot enough to melt and vitrify even the most stubborn materials, turning them into inert, rock-like solids that are completely safe and stable.
Imagine a solar-powered furnace that consumes no fuel, emits no greenhouse gases, and operates entirely off the grid. This isn’t science fiction — it’s already functioning.
Turning toxic waste into building blocks
Heliosand’s furnace is more than a clever concept. It’s a viable, ecological alternative to incineration. The system doesn’t require any fossil fuels, and the extreme heat it generates can be captured and reused, for example, to produce electricity or hydrogen.
And the waste? Once treated, it becomes inert and construction-grade material — a substitute for traditional mineral aggregates used in cement. In other words, dangerous waste is reborn as building material, closing the loop in a clean and effective way.
Sustainable, scalable — and surprisingly profitable
The environmental impact is obvious, but Heliosand’s model also makes solid economic sense. Thanks to free solar energy and a highly efficient process, the plant can pay for itself in just 100 days — a rare feat in the waste treatment world.
It’s a scalable solution too, one that could radically transform how the world deals with hazardous materials. For countries facing mounting waste challenges and limited landfill space, this kind of approach is not just innovative — it’s vital.
Born from a technical challenge — and a refusal to compromise
Back when Heliosand first envisioned its Fresnel lens system, the technology to build such a large-scale lens simply didn’t exist. The market only offered versions up to 10 square meters (about 108 sq ft). But rather than scale back their vision, the team at Heliosand went back to the drawing board and developed a patented, low-cost method to manufacture their own lenses in-house. That breakthrough was the key to making the entire project viable.
And the results speak for themselves. Heliosand’s technology can avoid up to 1.5 metric tons (approx. 3,300 lbs) of CO₂ equivalent emissions for every ton of waste treated, and can trap an additional 0.5 tons (1,100 lbs) of carbon dioxide directly in the vitrified material.
In an era desperate for real, circular solutions to climate change, this is more than promising — it’s visionary.
Source: Heliosand.com